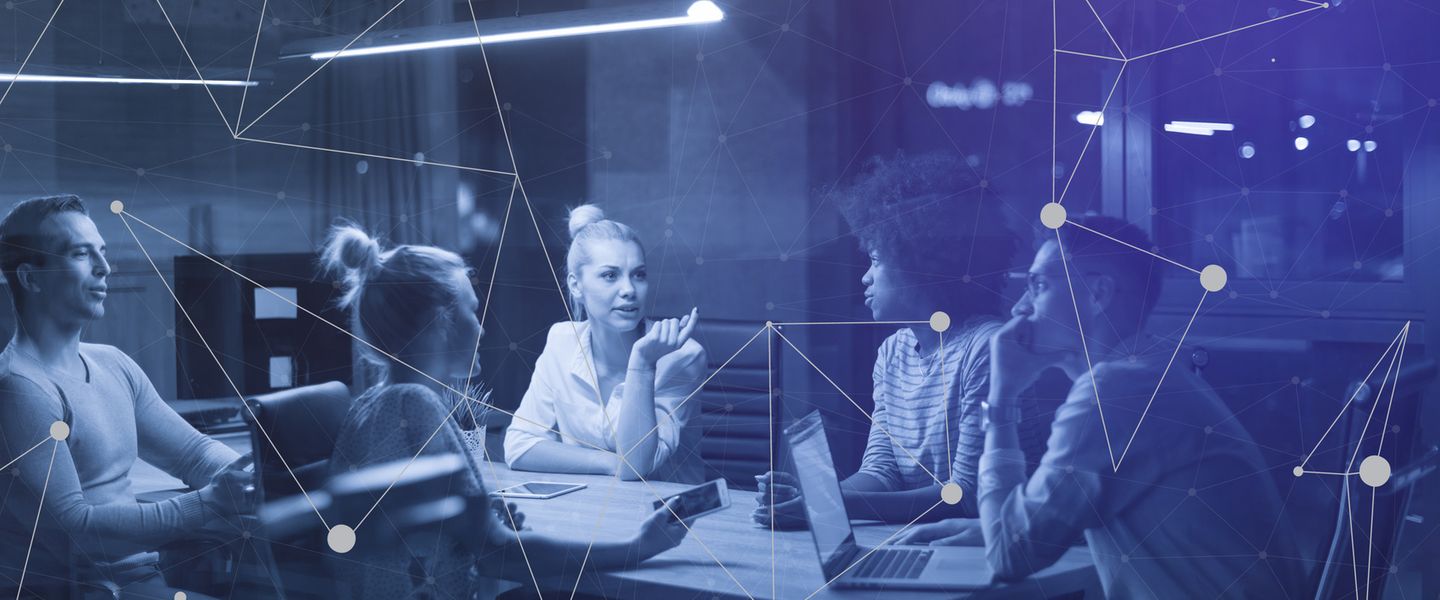
Big businesses don’t struggle in the same way when it comes to certain operations, as sometimes small businesses do. This is because you’ll often find big businesses have various departments with many skilled individuals who have extensive experience in managing specific business functions.
The role of operations management within a big business, for example; is a streamlined process headed up by one, or perhaps a few, experienced and highly knowledgeable operations managers. Most times there’s a team of people supporting the managers’ operational objectives by constantly seeking out ways to improve business operations. With a core team, it becomes a lot easier to find solutions and fully optimise operations.
The role of operations management in small businesses on the other hand often lacks a clear-cut process, usually developed through trial and error, and often managed by the business owner themselves, or a manager who is less knowledgeable on how to effectively manage operations. Unfortunately, this is usually because small businesses lack funds, especially during the startup phase.
With the role of operations management being a critical function within a business, what are small businesses to do if they’re unable to hire an experienced operations manager, but want to improve business operations and achieve a streamlined process? Well, the trick is, in fact, going back to basics, and finding a logical step by step method of managing the operational processes.
Take a look at these 5 essential techniques you can learn and implement today, to better manage operations within your small business:
1. Assess each task
The best way to assess a task is by breaking it up by asking vital questions. Firstly, find the source of the work – where does the work come from? Is it from a client, is it from the supervisor, the vendor? This will give you an idea of the nature of the task and how it should be handled.
Secondly, evaluate the process of that specific task. If it’s a work order for example; break down the process of how this task is managed by detailing each step: add up the charges of the work order, enter the values into the computer and hold it for payment from the customer etc. Creating a process is an incredibly important step.
Then, decide on how the work is stored. Is it filed in a personal client folder? Should it be stored away? Through assessing tasks it’s easier to create a process and identify the kind of person suitable for the job; as well as to better create job descriptions and worker manuals.
2. Prioritise tasks
Prioritising tasks is not just about creating a deadline – that comes later on. This covers the sequence of the task; which is also concerned with the creation of the process. Thereafter, tasks can be prioritised according to importance as well as the deadline – which can be managed by the employee themselves. When people have a clear indication of timelines and are aware of priorities they are able to streamline the process for themselves; resulting in a more efficient operation – even without much help from the operations manager.
3. Delegate accordingly
After you, as the manager, have assessed the task and have prioritised the sequence of workflow, you’ll have a good understanding of the perfect type of employee who will be able to carry out the task effectively and efficiently. You’ll know the skills and strengths that the task demands, and you’ll need to align this with those of the employee. Assigning the task to a person within the team who you think will best fit the requirements is called delegating.
4. Evaluate outcomes
Once the task is complete, it’s important that you evaluate the outcomes – especially in the beginning. Be careful not to look like you are micromanaging – it could come across that way if you continue evaluating results every single time after a task is complete, for months on end. Spot evaluations work more effectively as it does not threaten the employee.
5. Find solutions to areas of concern
After evaluating the outcomes, you will have a good idea of where the weak areas in the processes are. It could be a weakness in the work sequence, or even in the employees’ ability to carry out the job. Whatever the concerns are, you will need to find alternative solutions for them; which will hopefully better the operations. Remember that you should be committed to constant improvement – even a solution could prove to be ineffective.